Cavitation, heat generation, vibrations, acoustics – keywords for the design of a turbomachine that are indispensable for increasing the efficiency.
In addition to a detailed visualisation of the velocity and pressure distributions in the turbomachine, simulations are used to determine in particular the hydraulic efficiency, temperature fields, flow-induced static and dynamic component loads and vibrations, bearing forces, material removal (erosion) and acoustic effects. The precise knowledge of these parameters and their interactions allow highly efficient evaluations and simulation-based optimisations of the machines or their components.
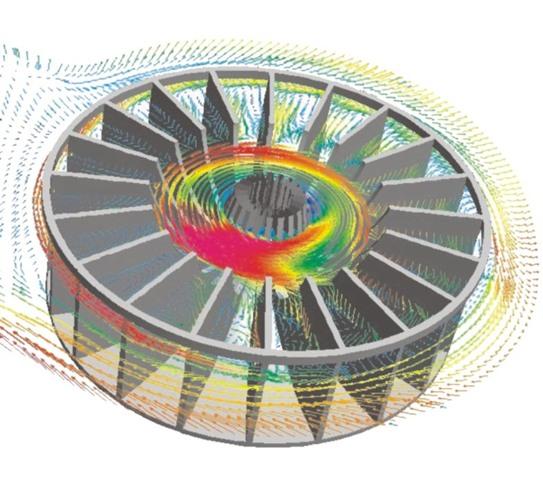
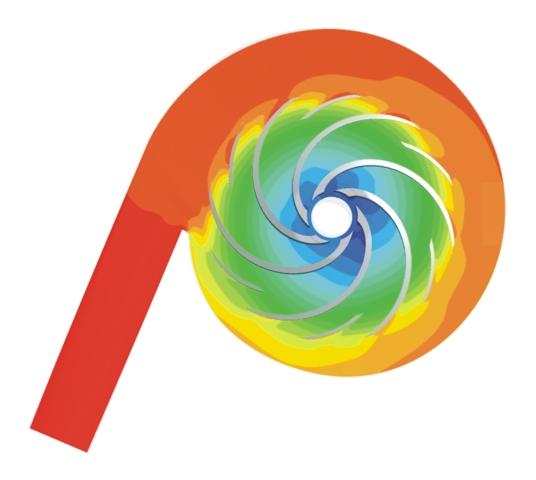